OUR DIE CASTING TOOLING SERVICES
Die casting tooling are crucial for the success of die casting production. Before tool manufacturing, we engage in general discussions and reviews with clients to assess the feasibility of tool part designs and rectify any existing flaws. Modifying tool features upfront not only helps improve the final parts but also enhances the quality of the tool itself. During this design phase, we can assess where removable components can be placed in the tooling, saving time and reducing maintenance for our clients.
Sunrise Metal With in-house tooling shop, offering clients a comprehensive solution from design, manufacturing, modification, and maintenance to end-of-tooling management. From conceptual visualization and functional analysis to tool design and validation, we support your project every step of the way.
WHY CHOOSE SUNRISE METAL DIE CAST TOOLING SERVICES (3)
INDUSTRIES EXPERIENCE
We’ve gained rich experience across various industries like medical, maritime, electronics, automotive, and general industry, enabling us to flexibly meet the diverse needs of our clients.We’re also happy to help you realize your imagined requirements.
PART GALLERY
OUR OTHER SERVICES
When casting meets Makino machine, parts with a precision of up to 15μ are born.
Instantly get your ideal prototype,speed up product launch, and save time and costs.
When castings undergo different surface treatments, will become adaptable to different environments.
Products that have undergone leak testing ensure that projects with sealing requirements are foolproof.
SUNRISE QUALITY SYSTEMS
Our company implements the ISO 9001 quality management system to optimize processes, enhance efficiency, and ensure that our products and services meet customer needs and expectations.
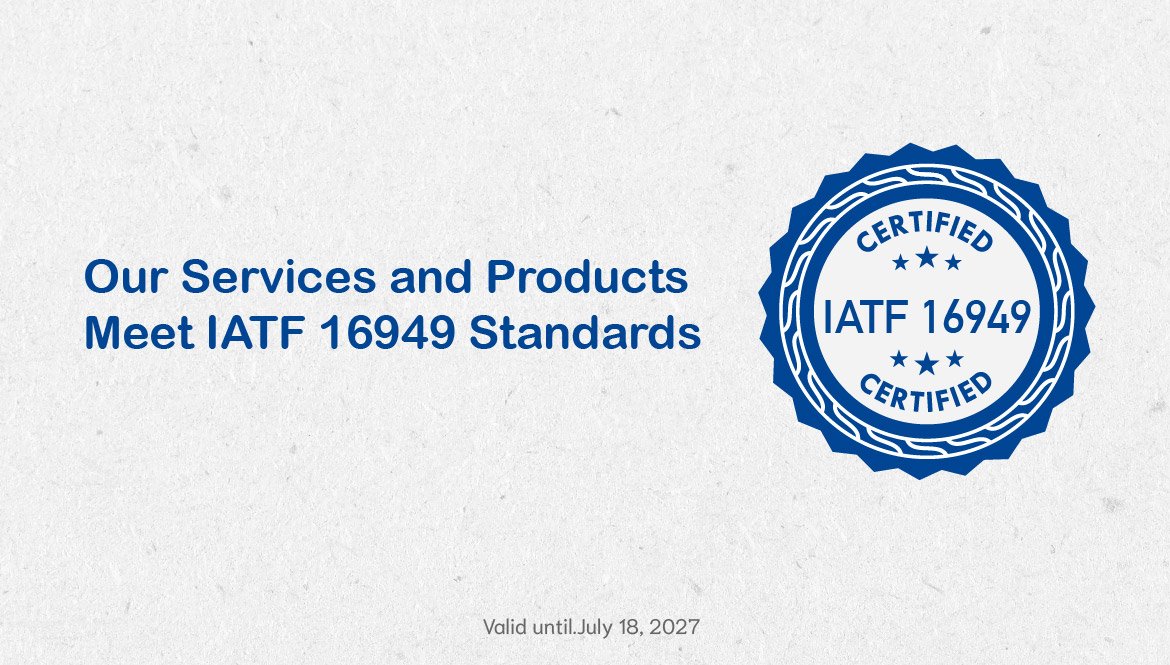
Our company strictly adheres to the IATF 16949 standard to ensure that our die-cast components meet the stringent requirements of the automotive industry and continuously improve our manufacturing processes and product quality.
Our company follows the ISO 13485 standard to ensure that our die-cast components meet the quality and safety requirements of the medical industry, thereby providing customers with reliable and safe medical devices.
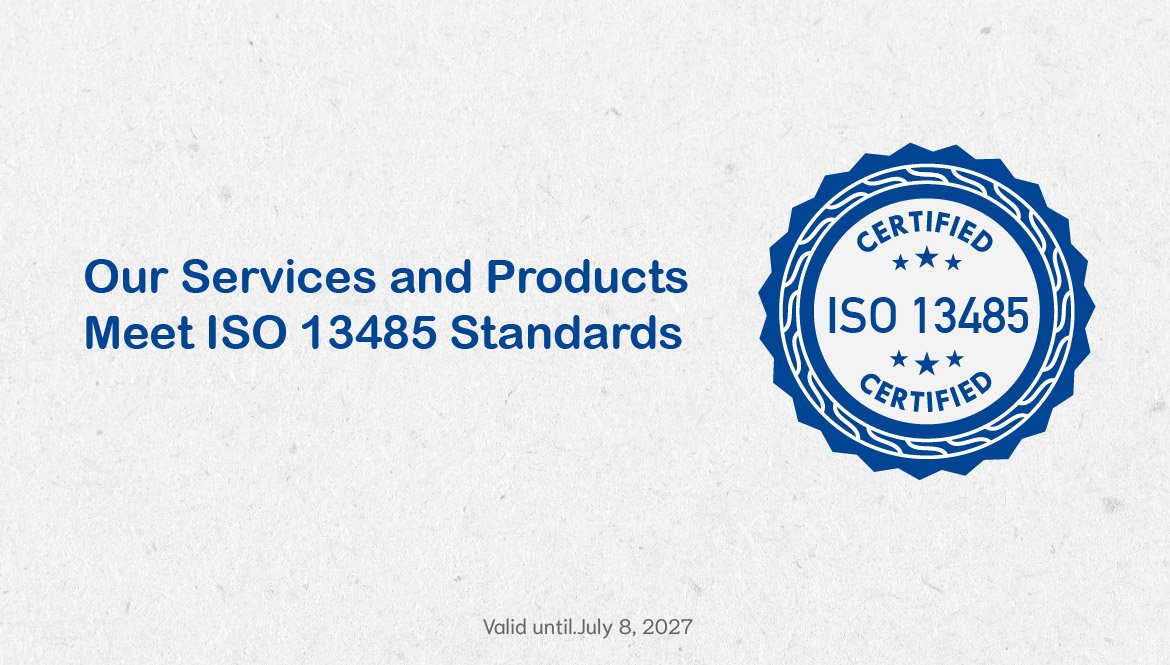
RELATED BLOG
The production time typically depends on the complexity and scale of the tool. Generally, a simple tool may take 4-6 weeks, while a complex tool may require 8 weeks or longer.
The cost of a tool varies depending on several factors, including design complexity, material selection, and manufacturing processes. Our tooling costs typically range from a few thousand to tens of thousands of dollars, with the exact price determined by project requirements.
The lifespan of a tool depends on several factors, including material selection, production volume, and frequency of use. Generally, our tools can withstand 50,000 to 100,000 injection cycles.
Yes, typically we provide samples for confirmation after the tool is completed. Customers can test and evaluate the samples to ensure the tool meets their expected requirements and specifications.
We strictly adhere to quality control procedures, including raw material inspection, process monitoring, and final testing. We utilize advanced equipment and technology to ensure that every tool meets our customers’ quality standards.